A new factory is up and running that will see hundreds of electric trains roll off the assembly line and onto India's famous railways. And it's Keller India that's played a vital role in it opening on time, coming up with an innovative foundation solution for this 100,000m2 site.
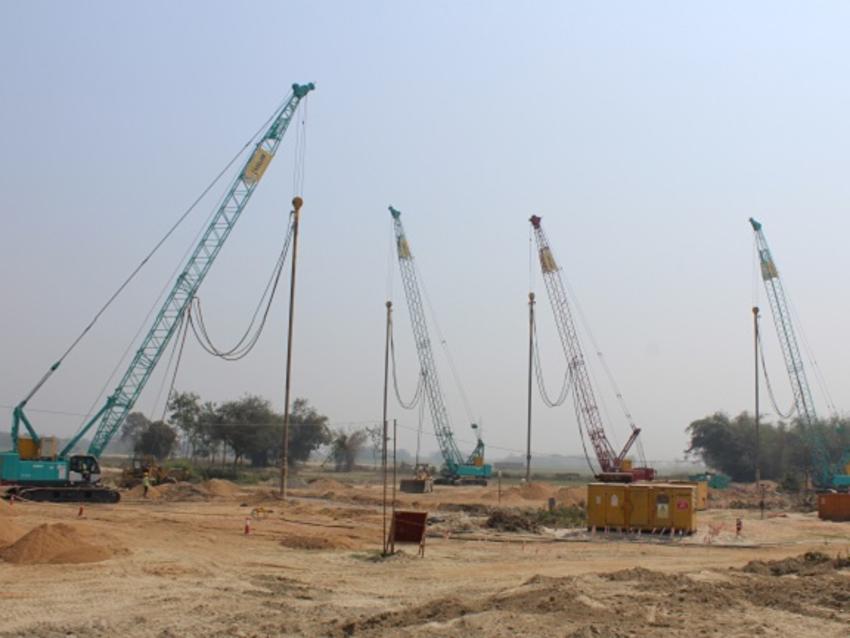
A new factory is up and running that will see hundreds of electric trains roll off the assembly line and onto India’s famous railways. And it’s Keller India that’s played a vital role in it opening on time, coming up with an innovative foundation solution for this 100,000m2 site.
With Indian Railways needing new technology to upgrade its British-era locomotive factories, the Indian Government launched a bidding process for foreign investment in 2014.
Thirty-year public-private partnerships were awarded to global giants Alstom and GE to build two new production plants in the far eastern state of Bihar, close to the Nepal and Bangladesh borders. These ventures will create hundreds of jobs, improve infrastructure and allow speeds of 120kph.
For its site in Madhepura, Alstom awarded its construction contract to Tata Projects Limited, a subsidiary of India’s largest conglomerate, Tata Group. With an estimated $4 billion investment and a need to deliver 800 electric engines in the next 11 years, Alstom was looking to move quickly. Tata, therefore, faced a tight schedule to get the plant built and operational in what is a remote location. Foundations needed to be prepared in just a few months, and while others were looking at piling as an option, Keller India’s experience in the region led to it offering a faster, more cost-effective solution: vibro compaction.
The power of the group
“Ground conditions in that part of the country are predominantly sandy due to alluvial river deposits,” explains Keller India Director Deepak Raj. “And with Madhepura in an earthquake zone, vibro compaction solution was the optimal solution for this situation. Also, piling solution would have been more expensive and taken seven to eight months to complete, whereas our solution would take just five. Additionally, our solution allowed a very low carbon footprint compared to the other techniques. We gave a presentation directly to Alstom together with Tata Projects to explain why this was the best option, and it convinced them.”
Keller was awarded the contract and faced immediate pressure to mobilize quickly. But even though they had a solution, the team faced several challenges. “Vibro compaction is uncommon in India – there are probably only a couple of companies that offer it – and even for us it wasn’t a routine technique,” Deepak says. “To improve 20m deep sandy deposits and to complete on time, we needed four 100-metric-tonne crawler cranes. With poor rental services in the area, we leveraged the power of the Keller Group to buy two new Kobelco crawler cranes. This demonstrated to our client that we had the best, most reliable machines.”
The cranes also needed to be fitted with specialist Vibrofloats tools, but with none available in India or the wider APAC region, the team had six (two for back-up) flown in specially from in-house equipment manufacturer KGS.
Delivered on time
After a month of mobilisation and testing to perfect the technique, crews worked virtually around the clock to meet the tight schedule. The delivery was phased out in grids which allowed Tata Projects to start the concrete works in parallel.
With all Keller projects safety is paramount, and despite scheduling pressure this one was no different. Between November and January, Madhepura experiences temperatures as low as 4ºC and heavy fog in the early morning and late at night. Additional safety equipment such as lighting and back horns were used and work stopped if conditions were too bad.
As promised, Keller delivered the project – which also included foundations for a four-storey living space for factory employees – on time and without incident.
More opportunities to come?
For Keller India, the project has been tremendously successful. Deepak says the company has won praise from two significant clients in Tata Projects and Alstom – and the team have had the chance to present the technique to Indian Railways senior leaders, who are responsible for so many important contracts.
“We’ve demonstrated that not only can we deliver a project on time, under significant pressure, but we can also act as a real partner, offering innovative solutions,” he says. “We met our project-specific financial targets and we’re confident this success will bring us more opportunities in the future.”